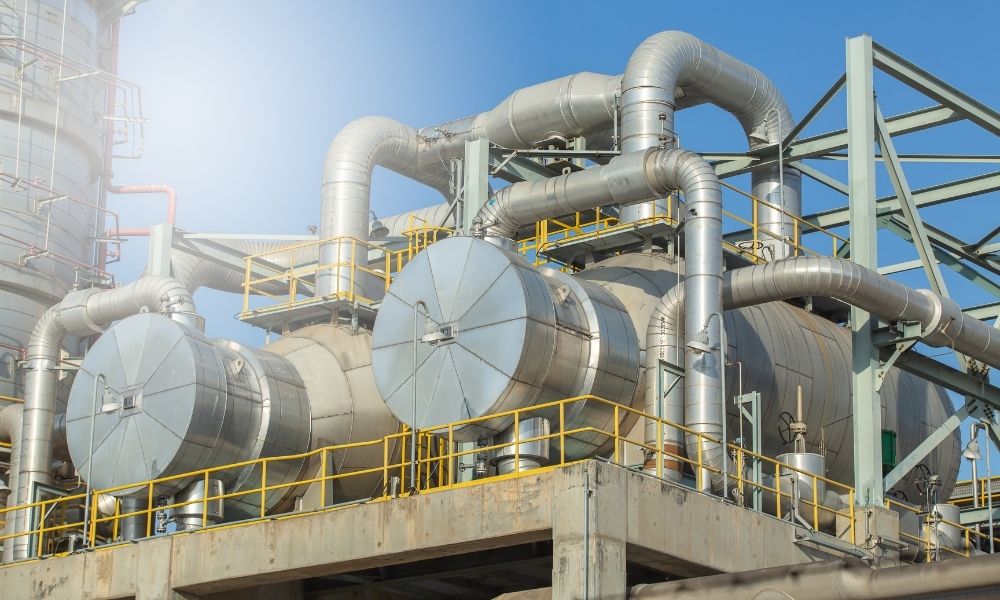
In the realm of industrial equipment, precision cooling is a critical component for ensuring the efficient and reliable operation of manufacturing processes. One technology that has emerged as a game-changer in this domain is the Microchannel Heat Exchanger. In this article, we will delve into the applications of Microchannel Heat Exchangers in manufacturing, exploring how these innovative heat exchange systems contribute to precision cooling, enhance efficiency, and address the unique thermal management challenges faced by industrial processes https://www.kaltra.com/microchannel-heat-exchangers.
Microchannel Heat Exchangers: Engineering Precision for Precision Cooling
Optimizing Heat Transfer Efficiency:
At the core of Microchannel Heat Exchangers is a design that focuses on optimizing heat transfer efficiency. The microscale channels within these heat exchangers provide a larger surface area for heat exchange, facilitating rapid and precise cooling in manufacturing processes.
Compact Design for Space Efficiency:
Microchannel Heat Exchangers are characterized by their compact design, making them well-suited for integration into manufacturing systems with limited space. The microscale channels allow for efficient space utilization, addressing the spatial constraints often encountered in industrial settings.
Materials Excellence for Durability:
Crafted from high-grade materials such as advanced aluminum or copper alloys, Microchannel Heat Exchangers offer not only exceptional thermal conductivity but also durability and reliability. This is crucial for withstanding the rigors of industrial environments and ensuring consistent performance.
Applications of Microchannel Heat Exchangers in Manufacturing
Metalworking Processes:
Precision cooling is vital in metalworking processes where maintaining specific temperatures is crucial for the quality and integrity of the final product. Microchannel Heat Exchangers efficiently dissipate heat generated during processes such as welding, forging, and casting, ensuring precise control over material properties.
Plastic Injection Molding:
Precision in cooling is a critical factor in plastic injection molding. Microchannel Heat Exchangers contribute to maintaining optimal temperatures during the molding process, improving cycle times and enhancing the quality of molded products.
Electronics Manufacturing:
The electronics manufacturing industry relies heavily on precision cooling to ensure the reliability and performance of electronic components. Microchannel Heat Exchangers play a key role in dissipating heat generated by circuit boards and electronic devices, preventing overheating and ensuring consistent operation.
Pharmaceutical Production:
Precision cooling is essential in pharmaceutical manufacturing, particularly in processes involving the synthesis and formulation of drugs. Microchannel Heat Exchangers contribute to maintaining specific temperatures in reactors and other equipment, ensuring the quality and efficacy of pharmaceutical products.
Advantages of Microchannel Heat Exchangers in Manufacturing Processes
Rapid and Uniform Cooling:
Microchannel Heat Exchangers excel in providing rapid and uniform cooling. The microscale channels promote turbulent flow, enhancing convective heat transfer and ensuring that manufacturing processes benefit from precise temperature control.
Energy Efficiency:
The efficient heat transfer capabilities of Microchannel Heat Exchangers contribute to energy efficiency in manufacturing. By optimizing the cooling process, these heat exchangers help reduce overall energy consumption, aligning with the growing emphasis on sustainable and cost-effective industrial practices.
Space Optimization:
The compact design of Microchannel Heat Exchangers allows for efficient space utilization in manufacturing facilities. This is particularly advantageous in industries where floor space is at a premium, allowing for flexible integration into existing systems.
Adaptability to Various Processes:
Microchannel Heat Exchangers are adaptable to a wide range of manufacturing processes. Their versatility and customization options make them suitable for diverse applications, allowing manufacturers to tailor the heat exchangers to the specific thermal management needs of their processes.
Considerations for Implementing Microchannel Heat Exchangers in Manufacturing
Process-Specific Requirements:
Understanding the specific thermal management requirements of each manufacturing process is crucial when implementing Microchannel Heat Exchangers. Factors such as temperature ranges, heat loads, and cooling rates should be carefully considered.
Fluid Compatibility:
Ensuring compatibility with the fluids used in manufacturing processes is essential for the longevity and effectiveness of Microchannel Heat Exchangers. This consideration contributes to the overall reliability of the system.
Integration with Control Systems:
Microchannel Heat Exchangers can be seamlessly integrated into existing control systems, providing manufacturers with the ability to monitor and adjust cooling parameters in real-time. This integration enhances the precision and efficiency of the overall manufacturing process.
Conclusion: Precision Cooling Redefined with Microchannel Heat Exchangers
In conclusion, Microchannel Heat Exchangers stand as a cornerstone in the realm of precision cooling in manufacturing. Their engineering precision, compact design, and versatility make them indispensable for addressing the unique thermal management challenges faced by industrial processes. As manufacturing industries continue to prioritize efficiency, reliability, and sustainability, the adoption of Microchannel Heat Exchangers is poised to redefine precision cooling standards, driving innovation and progress in the ever-evolving landscape of industrial equipment.